Xiamen Zopin New Material Limited Established in 2011, it is a new material industry with capabilities of independent research & development, production and sales as one. Our ISO9001:2012 factory covers an area of 6 hectares and a building area of 28,000 square meters, with annual production of high-performance metal foams of 250,000 square meters. Our R&D team is composed of academicians and experts from Tsinghua University, Polytechnic University of Hong Kong, Nanyang Technological University, and other domestic and foreign metal foam professionals. After many years’ endeavor, we now own our proprietary intellectual property rights in manufacturing high purity and high porosity metal foams.
Foamed Nickel: A Comprehensive Guide
Foamed nickel, also known as nickel foam or reticulated nickel foam, is a lightweight, porous material with an interconnected opencell structure. It combines the excellent properties of nickel—such as high electrical and thermal conductivity, corrosion resistance, and mechanical strength—with the unique characteristics of a foamlike material, including high porosity and large surface area. Below is an indepth exploration of foamed nickel, its production, applications, and key considerations.
●1. What Is Foamed Nickel?
Foamed nickel is a threedimensional, porous material made from pure nickel or nickel alloys. Its structure consists of a network of interconnected pores (cells) that provide:
High Surface Area: Ideal for catalytic reactions, energy storage, and filtration.
Uniform Porosity: Ensures consistent performance across the material.
Mechanical Strength: Despite its lightweight nature, it can withstand significant mechanical stress.
The porosity of foamed nickel typically ranges from 70% to 98%, depending on the application requirements.
●2. How Is Foamed Nickel Produced?
Foamed nickel can be produced using several methods, each offering unique advantages and limitations. The most common techniques include:
A. Electroplating
Process: A sacrificial template (e.g., polyurethane foam) is coated with nickel through electroplating. After deposition, the template is removed, leaving behind a nickel foam replica.
Advantages: High precision, costeffective for largescale production.
Limitations: Dependent on the availability of suitable templates.
B. Powder Metallurgy
Process: Fine nickel powder is mixed with binders, shaped into a foamlike structure, and sintered to form a solid material while maintaining porosity.
Advantages: Suitable for complex shapes, customizable porosity.
Limitations: Higher production costs compared to electroplating.
C. Replication Casting
Process: Molten nickel is poured into a porous template (e.g., ceramic or polymer), allowed to solidify, and then the template is removed.
Advantages: Produces dense and strong foam structures.
Limitations: Requires high temperatures, increasing energy consumption.
D. Additive Manufacturing (3D Printing)
Process: Nickel powder or wire is deposited layer by layer using advanced 3D printing techniques like direct metal laser sintering (DMLS) or electron beam melting (EBM).
Advantages: Highly customizable designs, reduced material waste.
Limitations: High initial investment, slower production speeds.
●3. Key Properties of Foamed Nickel
| Property | Description |
|||
| Electrical Conductivity | Excellent conductor, ideal for electrical applications. |
| Thermal Conductivity | High thermal conductivity for efficient heat transfer. |
| Corrosion Resistance | Resistant to corrosion in alkaline and certain acidic environments. |
| Porosity | Typically 70%–98%, providing a large surface area. |
| Mechanical Strength | Lightweight yet strong, suitable for structural applications. |
| Surface Area | Large surface area enhances catalytic and energy storage capabilities. |
High Purity Iron Nickel Foam
●4. Applications of Foamed Nickel
Foamed nickel's unique combination of properties makes it suitable for a wide range of applications across various industries:
A. Energy Storage
Batteries: Used as electrodes or current collectors in nickelmetal hydride (NiMH) batteries and lithiumion batteries.
Supercapacitors: Provides a conductive substrate with high surface area for efficient energy storage.
B. Catalysis
Serves as a support material for catalysts in chemical reactions, such as hydrogen production via water electrolysis.
C. Filtration
Ideal for industrial filters that remove particles, droplets, or contaminants from gases or liquids.
D. Heat Exchangers
Utilized in thermal management systems due to its excellent thermal conductivity and ability to facilitate efficient heat transfer.
E. Electromagnetic Interference (EMI) Shielding
Effective in shielding electronic devices from electromagnetic interference due to its high electrical conductivity.
F. Aerospace and Defense
Used in lightweight structural components, heat shields, and fuel cell systems.
G. Biomedical Engineering
Potential use in tissue scaffolds and implants due to its biocompatibility and mechanical strength.
●5. Advantages of Foamed Nickel
| Advantage | Description |
|||
| High Electrical Conductivity | Ideal for electrical applications requiring efficient electron transfer. |
| Good Thermal Conductivity | Effective for thermal management in hightemperature environments. |
| Corrosion Resistance | Resistant to corrosion in alkaline and certain acidic environments. |
| Large Surface Area | Beneficial for catalytic reactions and energy storage. |
| Customizability | Available in various densities, porosities, and shapes. |
| Proven Reliability | Backed by decades of research and development in nickel materials. |
●6. Limitations of Foamed Nickel
| Limitation | Description |
|||
| Cost | High production costs due to the complexity of manufacturing processes. |
| Fabrication Challenges | Requires specialized equipment and techniques for precise control over porosity and cell size. |
| Weight | Heavier compared to materials like carbon foam or titanium foam. |
| Limited Corrosion Resistance | May corrode in strongly acidic environments. |
●7. Comparison of Foamed Nickel with Other Materials
| Material | Key Features | Applications |
||||
| Foamed Nickel | High conductivity, corrosion resistance, customizable porosity | Batteries, filtration, catalysis, aerospace |
| Carbon Foam | Lightweight, good thermal conductivity | Thermal management, energy storage |
| Titanium Foam | Lightweight, excellent corrosion resistance | Aerospace, biomedical engineering |
| Aluminum Foam | Lightweight, good thermal conductivity | Automotive, construction |
●8. Future Trends in Foamed Nickel
1. Advanced Manufacturing Techniques:
Innovations in additive manufacturing and nanostructuring are expected to enhance the performance and affordability of foamed nickel.
2. Sustainability:
Development of ecofriendly production methods and recyclable materials will reduce environmental impact.
3. Hybrid Composites:
Integration of foamed nickel with other materials (e.g., polymers, ceramics) will expand its applications in fields like biomedical engineering and smart materials.
4. Emerging Applications:
Growing demand for renewable energy, aerospace, and automotive technologies will drive new uses for foamed nickel.
●9. Conclusion
Foamed nickel is a versatile and highperformance material with applications spanning energy storage, filtration, catalysis, and aerospace. While its production involves complex processes and higher costs compared to some alternatives, its unique combination of properties makes it indispensable for many critical applications. As advancements in manufacturing and material science continue, foamed nickel is poised to play an even more significant role in addressing global challenges related to energy, environment, and technology.
If you're exploring foamed nickel for your project, carefully evaluate its properties, production methods, and cost implications to ensure it meets your specific needs. For further details or assistance, feel free to ask!
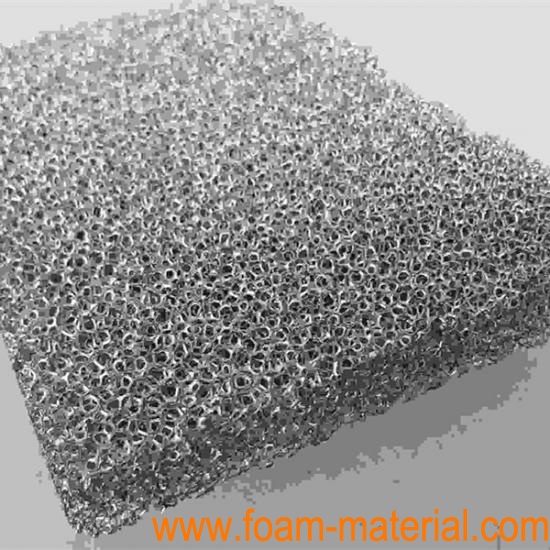