Xiamen Zopin New Material Limited Established in 2011, it is a new material industry with capabilities of independent research & development, production and sales as one. Our ISO9001:2012 factory covers an area of 6 hectares and a building area of 28,000 square meters, with annual production of high-performance metal foams of 250,000 square meters. Our R&D team is composed of academicians and experts from Tsinghua University, Polytechnic University of Hong Kong, Nanyang Technological University, and other domestic and foreign metal foam professionals. After many years’ endeavor, we now own our proprietary intellectual property rights in manufacturing high purity and high porosity metal foams.
Metal Mesh Sieve: A Comprehensive Guide
A metal mesh sieve is a specialized tool or component made from interwoven metal wires designed for filtration, separation, and screening applications. These sieves are widely used in industries such as mining, pharmaceuticals, food processing, chemical engineering, and more. Below is an in-depth exploration of metal mesh sieves, including their types, properties, manufacturing processes, applications, advantages, limitations, and future prospects.
●1. What Is a Metal Mesh Sieve?
A metal mesh sieve is a fine-woven or perforated structure made from metal wires or sheets. It is engineered to separate particles, liquids, or gases based on size, density, or other physical properties. The mesh sieve can be tailored to specific pore sizes and patterns to meet the requirements of various industrial processes.
Metal mesh sieves are available in different materials such as stainless steel, copper, nickel alloys, brass, and titanium, each offering unique characteristics suited to particular applications.
●2. Types of Metal Mesh Sieves
A. Woven Wire Mesh Sieves
Made by weaving metal wires into a fabric-like structure.
Available in plain weave, twill weave, or Dutch weave.
Suitable for fine filtration and particle separation.
B. Perforated Metal Sieves
Created by punching precise holes into flat metal sheets.
Ideal for applications requiring uniform openings and high strength.
C. Electroformed Metal Sieves
Produced using electroforming technology, where a thin layer of metal is deposited onto a mandrel to create a precise mesh pattern.
Offers extremely fine and consistent pore sizes.
Used in ultra-fine filtration and analytical applications.
D. Sintered Metal Sieves
Made by sintering metal powders or fibers together to form a porous structure.
Provides excellent mechanical strength and resistance to clogging.
Commonly used in high-pressure filtration systems.
●3. Properties of Metal Mesh Sieves
| Property | Description |
|-------------------------------|-----------------------------------------------------------|
| Precision | Capable of achieving very fine and consistent pore sizes. |
| Durability | Resistant to wear, corrosion, and environmental degradation. |
| Strength | High tensile strength, suitable for demanding applications. |
| Conductivity | Excellent electrical and thermal conductivity (depending on material). |
| Customizability | Available in various materials, pore sizes, and designs. |
●4. Manufacturing Processes
A. Weaving
Interlacing metal wires to create a fabric-like structure.
Suitable for fine meshes with small pore sizes.
B. Perforation
Punching holes into metal sheets using hydraulic presses or CNC machines.
Ensures uniform patterns and precise dimensions.
C. Electroforming
Depositing a thin layer of metal onto a mandrel to create a precise mesh pattern.
Ideal for ultra-fine filtration applications.
D. Sintering
Bonding metal powders or fibers under heat and pressure to form a porous structure.
Provides excellent mechanical strength and resistance to clogging.
Ag Metal Mesh
●5. Applications of Metal Mesh Sieves
A. Filtration
Used in industries like oil & gas, water treatment, and chemical processing to separate solids from liquids or gases.
Example: Fine woven wire mesh for filtering impurities in drinking water.
B. Particle Separation
Employed in mining, agriculture, and pharmaceuticals to classify particles by size.
Example: Vibrating screens with metal mesh sieves for grading sand or gravel.
C. Food Processing
Utilized in food production for tasks like straining, de-lumping, and powder classification.
Example: Stainless steel sieves for separating flour particles.
D. Analytical Testing
Used in laboratories for quality control and particle size analysis.
Example: Electroformed sieves for precise particle classification in R&D.
E. Industrial Screening
Applied in manufacturing processes to ensure product consistency and quality.
Example: Metal mesh sieves for screening powdered metals in additive manufacturing.
●6. Advantages of Metal Mesh Sieves
| Advantage | Description |
|-------------------------------|-----------------------------------------------------------|
| Precision | Capable of achieving very fine and consistent pore sizes. |
| Durability | Long-lasting and resistant to harsh environments. |
| Strength | High mechanical strength ensures reliable performance. |
| Versatility | Available in various materials and pore sizes. |
| Chemical Resistance | Many metals (e.g., stainless steel) resist corrosion. |
●7. Limitations of Metal Mesh Sieves
| Limitation | Description |
|-------------------------------|-----------------------------------------------------------|
| Cost | High-quality sieves (e.g., electroformed or sintered) can be expensive. |
| Maintenance | Requires regular cleaning to prevent clogging. |
| Weight | Heavier than polymer-based alternatives. |
| Complex Fabrication | Some sieve types require advanced manufacturing techniques. |
●8. Key Manufacturers and Research Institutions
| Organization | Focus Areas |
|------------------------------|---------------------------------------------------------|
| GKD (Gebhardt Drahtwaren)| Leading producer of metal meshes for industrial use. |
| W.S. Tyler | Specializes in sieves and screening solutions. |
| Mott Corporation | Expertise in precision filtration and sintered metals. |
| Fraunhofer Institute | Research on advanced materials and sieve technologies. |
●9. Future Trends in Metal Mesh Sieves
1. Advanced Materials:
Development of nanostructured meshes for improved filtration efficiency and reduced clogging.
2. Smart Sieves:
Integration of sensors or conductive elements for real-time monitoring of filtration performance.
3. Sustainability:
Focus on recyclable and environmentally friendly production methods.
4. Additive Manufacturing:
Use of 3D printing to create complex and customized sieve geometries.
5. Hybrid Structures:
Combining metals with polymers or ceramics for lightweight and durable designs.
●10. Conclusion
Metal mesh sieves are critical components in filtration, separation, and screening processes across various industries. Their precision, durability, and versatility make them indispensable for ensuring product quality and process efficiency. While challenges such as cost and maintenance exist, ongoing advancements continue to enhance their performance and expand their applications.
If you're considering metal mesh sieves for your project, carefully evaluate factors such as material selection, pore size, and application requirements to achieve optimal results.
For further details or assistance in designing or implementing metal mesh sieves, feel free to ask!
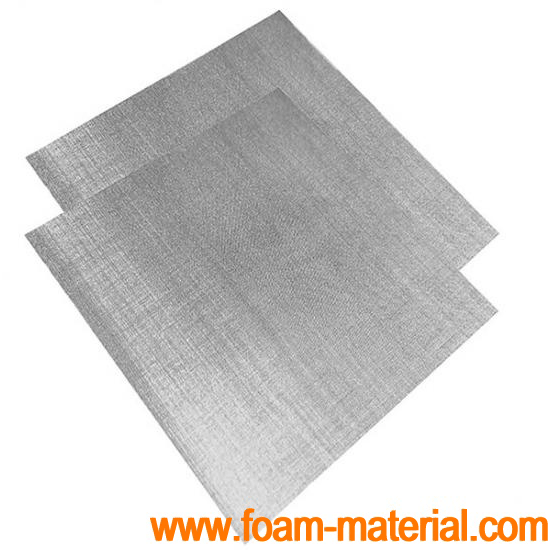