Xiamen Zopin New Material Limited Established in 2011, it is a new material industry with capabilities of independent research & development, production and sales as one. Our ISO9001:2012 factory covers an area of 6 hectares and a building area of 28,000 square meters, with annual production of high-performance metal foams of 250,000 square meters. Our R&D team is composed of academicians and experts from Tsinghua University, Polytechnic University of Hong Kong, Nanyang Technological University, and other domestic and foreign metal foam professionals. After many years’ endeavor, we now own our proprietary intellectual property rights in manufacturing high purity and high porosity metal foams.
Porous Copper Foam: Properties, Applications, and Advancements
Porous copper foam is a lightweight, threedimensional material with interconnected opencell structures. It combines the unique properties of copper—such as high electrical and thermal conductivity, excellent ductility, and good corrosion resistance in certain environments—with the advantages of porosity, including large surface areas and reduced weight. Below is a comprehensive overview of porous copper foam, its characteristics, applications, and current advancements.
●1. What Is Porous Copper Foam?
Porous copper foam is created by forming a network of copper struts or ligaments that define open pores. The porosity (typically ranging from 70% to 98%) provides a high surface areatovolume ratio, making it ideal for applications requiring enhanced contact surfaces, efficient heat transfer, or catalytic activity.
Key Characteristics:
High Electrical Conductivity: Copper's natural conductivity makes it suitable for electrical applications.
Excellent Thermal Conductivity: Ideal for heat exchangers and thermal management systems.
Mechanical Flexibility: Copper foam can be bent or shaped without losing structural integrity.
Corrosion Resistance: Performs well in alkaline environments but may oxidize in acidic conditions unless coated.
Customizable Porosity: Can be engineered with varying pore sizes and densities to suit specific needs.
●2. Manufacturing Methods for Porous Copper Foam
Several techniques are used to produce porous copper foam, each offering different advantages depending on the desired application:
A. Powder Metallurgy
Process: Copper powder is compacted and sintered to form a porous structure.
Advantages: Costeffective for largescale production; allows precise control over porosity and density.
Applications: Heat exchangers, filters, and electrodes.
B. Electrodeposition
Process: Copper is deposited onto a sacrificial template (e.g., polymer foam), which is later dissolved to leave behind a porous copper structure.
Advantages: Produces highly uniform and finepored foams with excellent mechanical strength.
Applications: Catalysis, battery electrodes, and sensors.
C. Additive Manufacturing (3D Printing)
Process: Copper is printed layerbylayer using advanced additive manufacturing techniques.
Advantages: Enables complex geometries and custom designs; reduces material waste.
Applications: Aerospace components, biomedical implants, and advanced electronics.
D. Chemical Vapor Deposition (CVD)
Process: Copper is deposited via chemical reactions at elevated temperatures.
Advantages: Produces highpurity copper foam with controlled microstructures.
Applications: Highperformance catalyst supports and electronic substrates.
●3. Applications of Porous Copper Foam
The versatility of porous copper foam makes it suitable for a wide range of industries and applications:
A. Energy Storage
Batteries: Copper foam serves as an electrode material or current collector due to its excellent electrical conductivity and stability.
Supercapacitors: Provides a large surface area for doublelayer capacitance and pseudocapacitance.
B. Heat Management
Heat Exchangers: Efficiently transfers heat due to its high thermal conductivity and large surface area.
Thermal Interfaces: Acts as a thermal interface material (TIM) to dissipate heat from electronic devices.
C. Filtration
Liquid Filters: Removes impurities from liquids while maintaining flow rates.
Gas Filters: Captures fine particles and contaminants from gases.
D. Catalysis
Chemical Reactions: Serves as a support material for catalysts in hydrogen production, CO₂ reduction, and other processes.
Water Electrolysis: Enhances the efficiency of electrolyzers by increasing active surface areas.
E. Biomedical Engineering
Tissue Engineering: Used as scaffolds for tissue growth due to its biocompatibility and mechanical flexibility.
Implants: Lightweight and strong, making it suitable for orthopedic implants.
F. Aerospace and Defense
Lightweight Structures: Reduces overall weight without compromising strength.
EMI Shielding: Provides effective electromagnetic interference shielding for sensitive electronics.
Thin Copper Foam
●4. Advantages of Porous Copper Foam
| Advantage | Description |
|||
| High Conductivity | Superior electrical and thermal conductivity. |
| Large Surface Area | Maximizes active sites for reactions and energy storage. |
| Mechanical Strength | Combines strength with flexibility for various applications. |
| Biocompatibility | Safe for use in biomedical devices and implants. |
| Customizability | Tailored porosity, thickness, and density for specific needs. |
●5. Challenges in Using Porous Copper Foam
Despite its benefits, there are challenges associated with porous copper foam:
| Challenge | Description |
|||
| Oxidation and Corrosion | Prone to oxidation in air and corrosion in acidic environments unless coated. |
| Cost | Advanced manufacturing techniques like 3D printing can increase costs. |
| Uniformity | Achieving consistent porosity and density across large areas can be difficult. |
| Weight | Heavier than lighter alternatives like aluminum foam. |
●6. Strategies to Enhance Performance
To address the limitations of porous copper foam, researchers have developed several strategies:
A. Surface Coatings
Applying protective coatings (e.g., nickel, gold, or ceramic layers) improves corrosion resistance and durability.
B. Hybrid Structures
Combining copper foam with other materials, such as graphene or carbon nanotubes, enhances mechanical strength and conductivity.
C. Advanced Manufacturing Techniques
Using technologies like additive manufacturing ensures precise control over geometry and porosity.
D. Functionalization
Modifying the surface of copper foam with functional groups or nanoparticles improves catalytic activity and specificity.
●7. Comparison with Other Porous Metals
| Material | Key Features | Applications |
||||
| Copper Foam | High conductivity, customizable porosity, good ductility | Batteries, heat exchangers, catalysis |
| Nickel Foam | Excellent corrosion resistance, high strength | Supercapacitors, filtration, aerospace |
| Aluminum Foam | Lightweight, costeffective | Automotive, packaging, construction |
| Titanium Foam | Excellent biocompatibility, corrosion resistance | Medical implants, aerospace |
●8. Future Trends and Innovations
The future of porous copper foam looks promising, driven by advancements in materials science and engineering:
1. Sustainable Production:
Developing ecofriendly methods to reduce environmental impact during manufacturing.
2. Advanced Composites:
Integrating copper foam with emerging materials like MXenes or metalorganic frameworks (MOFs) for enhanced performance.
3. Emerging Applications:
Growing demand in renewable energy, electric vehicles, and smart grids will drive new uses for copper foam.
4. Customized Solutions:
Advances in 3D printing and nanostructuring enable tailored solutions for specific industries.
●9. Conclusion
Porous copper foam is a versatile material with exceptional properties that make it indispensable in various industries. Its combination of high conductivity, large surface area, and mechanical flexibility positions it as a key player in energy storage, heat management, filtration, and biomedical applications. While challenges exist, ongoing research and development are addressing these limitations, paving the way for more efficient and sustainable solutions.
If you're exploring porous copper foam for your project, carefully evaluate factors such as application requirements, budget, and desired properties to ensure optimal results. For further details or assistance, feel free to ask!
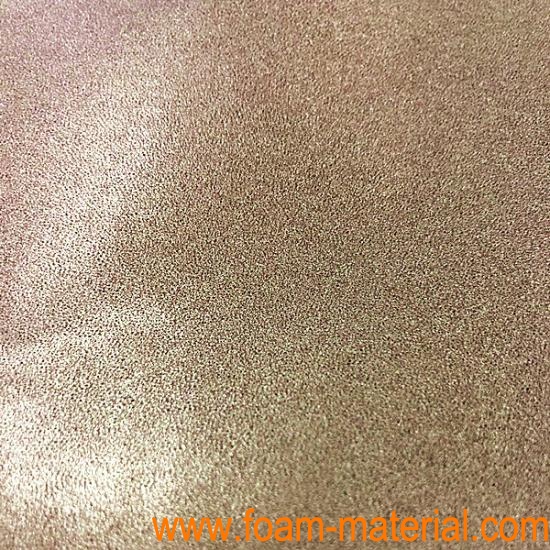