Xiamen Zopin New Material Limited Established in 2011, it is a new material industry with capabilities of independent research & development, production and sales as one. Our ISO9001:2012 factory covers an area of 6 hectares and a building area of 28,000 square meters, with annual production of high-performance metal foams of 250,000 square meters. Our R&D team is composed of academicians and experts from Tsinghua University, Polytechnic University of Hong Kong, Nanyang Technological University, and other domestic and foreign metal foam professionals. After many years’ endeavor, we now own our proprietary intellectual property rights in manufacturing high purity and high porosity metal foams.
Nickel Foam Cost: A Comprehensive Guide
Nickel foam is a highperformance material with excellent electrical, thermal, and mechanical properties, making it suitable for applications in energy storage, filtration, catalysis, aerospace, and biomedical engineering. However, its cost can vary significantly depending on factors such as production method, porosity, density, size, and application requirements. Below is an indepth exploration of the cost considerations associated with nickel foam.
●1. Factors Influencing Nickel Foam Cost
A. Production Method
The method used to produce nickel foam has a significant impact on its cost:
Electroplating: Generally more costeffective for largescale production due to its simplicity and ability to replicate templates efficiently. However, the cost of sacrificial templates (e.g., polyurethane) and postprocessing steps can add up.
Powder Metallurgy: This method tends to be more expensive due to the need for fine nickel powder, binders, and precise sintering conditions. It is often used for specialized applications requiring complex geometries or high precision.
Replication Casting: While this method produces dense and strong foams, it involves high temperatures and energy consumption, increasing costs.
Additive Manufacturing (3D Printing): This is typically the most expensive method due to the high cost of equipment, materials, and slow production speeds. However, it offers unparalleled customization and design flexibility.
B. Porosity and Density
Porosity: Higher porosity (e.g., 90%–98%) reduces material usage but may require additional processing to ensure structural integrity, affecting cost.
Density: Lowerdensity foams are generally less expensive due to reduced material content, but they may require reinforcement for certain applications.
C. Size and Shape
Larger or customshaped nickel foam pieces tend to be more expensive due to increased material usage and fabrication complexity.
Complex geometries, such as those produced via additive manufacturing, can significantly increase costs.
D. Surface Treatment and Coatings
Additional treatments like polishing, coating, or heat treatment to enhance properties (e.g., corrosion resistance or thermal stability) can add to the overall cost.
E. ApplicationSpecific Requirements
Nickel foam for critical applications (e.g., aerospace or biomedical engineering) may require stricter quality control, certification, and testing, driving up costs.
●2. Typical Cost Range of Nickel Foam
| Factor | Cost Range (per kg) |
|||
| Electroplated Nickel Foam | $50–$150 |
| Powder Metallurgy Foam | $100–$300 |
| Replication Casting Foam | $150–$400 |
| Additive Manufacturing Foam| $500–$1,500+ |
Note: These costs are approximate and can vary based on supplier, region, and specific requirements.
●3. Breakdown of Nickel Foam Costs
A. Raw Material Costs
Nickel: Nickel is a relatively expensive metal, with prices fluctuating based on market conditions. As of 2023, nickel prices ranged from $20,000 to $30,000 per metric ton ($20–$30 per kg).
Alloys: Adding alloying elements (e.g., chromium or iron) increases material costs but improves properties like corrosion resistance.
B. Manufacturing Costs
Labor: Skilled labor is required for processes like electroplating, sintering, and additive manufacturing.
Equipment: Hightech equipment, especially for additive manufacturing, adds to the overall cost.
Energy: Energyintensive processes like replication casting or sintering further increase costs.
C. PostProcessing Costs
Surface Treatments: Coatings, polishing, or other surface treatments can add 10%–30% to the total cost.
Quality Control: Rigorous testing and inspection, particularly for critical applications, increase costs.
High Porosity nickel Foam
●4. Strategies to Reduce Nickel Foam Costs
A. Optimize Design
Simplify designs to minimize material usage and reduce fabrication complexity.
Use simulation tools to optimize porosity, density, and cell size for specific applications.
B. Choose the Right Production Method
For largescale applications, electroplating is often the most costeffective option.
For small batches or custom shapes, additive manufacturing may be justified despite higher costs.
C. Source Locally
Reducing transportation costs by sourcing nickel foam locally can lower overall expenses.
D. Explore Alternatives
Consider alternative materials or hybrid composites if cost is a major constraint. For example, carbon foam or titanium foam may offer similar properties at a lower cost.
●5. Comparison with Other Materials
| Material | Typical Cost (per kg) | Key Advantages | Key Disadvantages |
|||||
| Nickel Foam | $50–$1,500+ | Excellent conductivity, corrosion resistance | High cost, limited scalability |
| Carbon Foam | $20–$100 | Lightweight, good thermal conductivity | Lower electrical conductivity |
| Titanium Foam | $100–$500 | Lightweight, excellent corrosion resistance | Expensive raw material |
| Aluminum Foam | $30–$200 | Lightweight, good thermal conductivity | Poor corrosion resistance |
●6. Future Trends in Nickel Foam Cost
1. Advances in Manufacturing Technology:
Innovations in additive manufacturing and automation could reduce production costs over time.
2. Economies of Scale:
Increased adoption of nickel foam across industries may lead to lower costs through mass production.
3. Sustainability Initiatives:
Development of recyclable nickel foam or ecofriendly production methods could help reduce longterm costs.
4. Alternative Materials:
Advances in alternative materials (e.g., graphenebased foams) may provide costeffective substitutes for certain applications.
●7. Conclusion
Nickel foam is a highperformance material with a wide range of applications, but its cost can be a significant consideration. The production method, porosity, size, and applicationspecific requirements all influence its price. By carefully evaluating these factors and exploring costreduction strategies, you can select the most economical option for your project.
If you're looking to purchase nickel foam or integrate it into your product, consult suppliers or manufacturers to get accurate pricing based on your specific needs. For further details or assistance, feel free to ask!
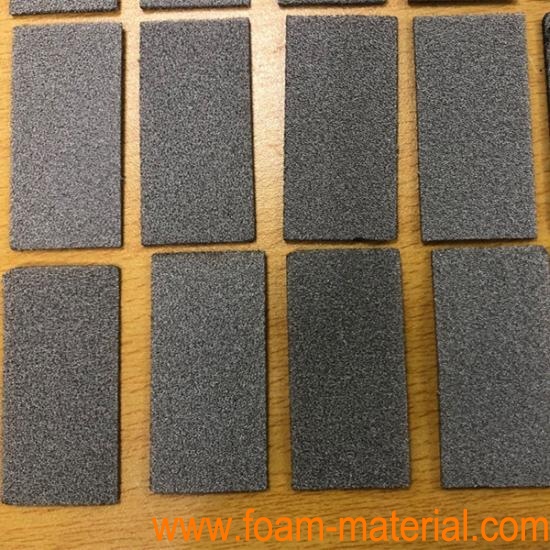